Integral System Helps French Factories Improve Equipment and Facility Management
1/1/2024
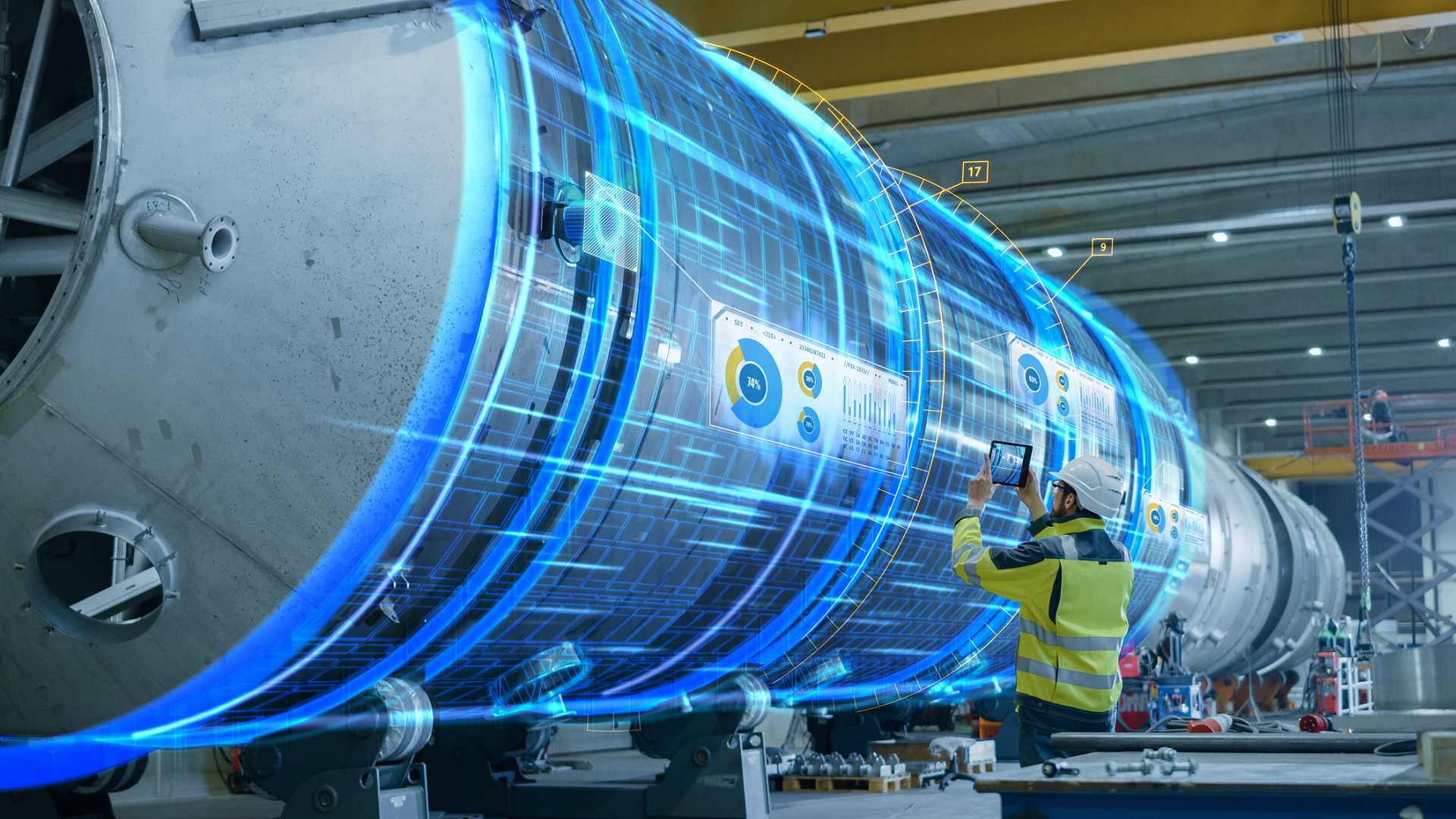
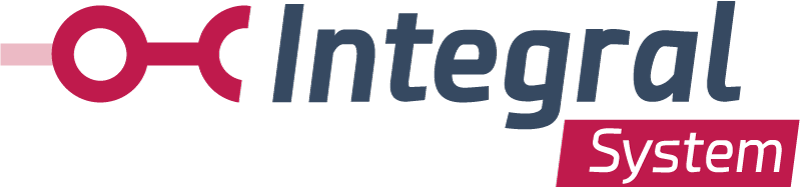
Despite advancements in smart manufacturing over the past decade, manufacturers in France continue to encounter significant challenges in implementing smart solutions. One key pain point is the aging infrastructure, which demands regular maintenance and repairs to minimize downtime and maintain productivity.
To overcome these challenges, Integral System and Advantech have joined forces in a close collaboration. Leveraging Advantech’s IoT hardware portfolio and modular, low-code/no-code software strategy, this collaboration is empowering factories in building sustainable industrial information systems.
A strong partnership for smart factory innovation
Integral System has a rich history of 20 years in distributing industrial computing solutions in France, focusing on providing personalized, sustainable, and high-quality solutions to their customers. Since 2006, they have been a valued channel partner of Advantech, enabling them to provide more effective solutions to their customers. In recognition of this close collaboration, Integral System became an Advantech Premier Partner in 2021 and WISE-IoT VIP partner in 2023. Moving forward, the two companies plan to deepen their cooperation by creating solutions for smart factories and provide it to their system integrator ecosystem
“Advantech’s position as a global leader in industrial computing solutions is strategic for our core business,” highlighted Vincent Gache, CEO of Integral System. He emphasized the significance of Advantech’s expertise in Industry 4.0 digitalization strategy, especially given the growing adoption of IIoT devices, data analytics, and AI technologies designed to help maintain and monitor industrial assets in real time. Transitioning from reactive to proactive management is a pivotal step for factories if they are to minimize unplanned downtime and equipment failures, and this is helping French manufacturers make significant advancements in their smart factory practices.
Improving equipment maintenance with iFactory/Maintenance and iFactory/PHM
Advantech’s iFactory/Maintenance and iFactory/PHM are highly viable solutions for factories. Elaborating on these solutions, Mr. Gache highlighted their three progressive steps for maintaining critical assets: scheduled maintenance activities, proactive maintenance to eliminate defects, and predictive maintenance to forecast future reliability.
“Motors play a critical role in the proper functioning of production lines,” stated Mr. Gache. He pointed out that the first step of scheduling regular maintenance to ensure optimal motor function can be achieved with iFactory/Maintenance. Through the seamless integration of iFactory/Maintenance and WISE/iMobile Services applications, all iFactory/Maintenance dashboards can be accessed on mobile phones, enabling administrators to plan equipment maintenance tours and coordinate maintenance tasks with field teams.
The second step is to implement a proactive maintenance strategy with iFactory/Maintenance. This can be as simple as establishing data collection points to measure motor usage intensity so maintenance operations can be adjusted based on current data.
The third step is to achieve predictive maintenance. Factories can install sensors such as Advantech’s WISE-2410 LoRaWAN Wireless Vibration Sensor and then transfer the motor data to iFactory/PHM so Advantech’s pre-trained AI models can be leveraged to help prevent malfunctions.
Moreover, each step of the process can trigger alert notifications to the concerned teams, in order to optimize reaction time and fluidify the information flows inside the factories
As one example, automotive manufacturers can leverage iFactory/Maintenance and iFactory/PHM to automate their maintenance processes. With predictive maintenance, factories can optimize their maintenance schedules, reduce maintenance costs, and improve the realibility of critical assets, thus improving equipment uptime and efficiency while minimizing risks due to unplanned downtime.
Another example is renewable energy companies, who can use iFactory/PHM to monitor and maintain the health of wind turbines, engines, generators, and more.
Integral System’s experience in industrial computing hardware and software engineering, combined with Advantech’s hardware, software, solutions, and cloud platform services for smart factories, enable them to create personalized, sustainable maintenance solutions.
iFactory/PHM
Proactively monitors machine health and predicts malfunctions, leading to improved uptime while reducing costs and extending the lifespan of equipment.
iFactory/Maintenance
Improve maintenance efficiency and reduces costs by providing real-time machine status information, preventive maintenance notifications, and automated scheduling, thus minimizing unplanned downtime while maximizing operational efficiency and ROI.
Quote : “Advantech's expertise in Industry 4.0 digitalization strategy and its position as a global leader in industrial computing solutions are strategically important for our core business.”- Vincent Gache, CEO of Integral System
WISE-IoT Magazine – Intelligent Factory: Transformation the Global Manufacturing Landscape with IoT
Advantech has remained committed to collaborating with global partners. Together, we strive to develop solutions that facilitate the rapid digital transformation of manufacturing while boosting competitive advantage.