AI Predict Maintenance for Wind Turbine Monitoring
20-02-2024
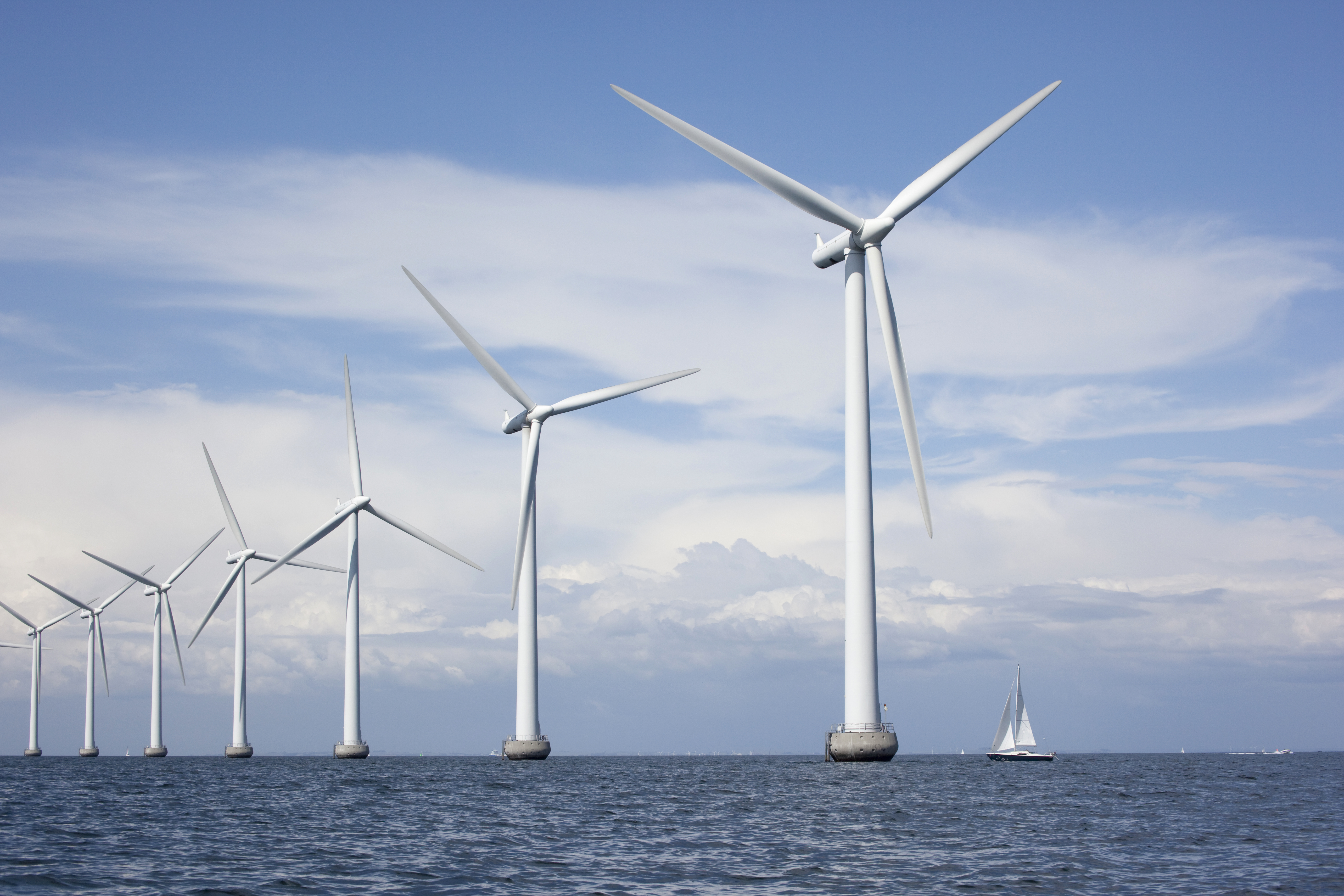
The Growing Trend and High Maintenance Cost in Wind Energy
In 2016, over 170 countries collectively signed the "Paris Agreement," committing to curb global warming and carbon emissions, aiming to limit the increase in the global average temperature to below 2°C above pre-industrial levels. Currently, more than 90 countries globally have set targets to achieve 50% of total electricity generation from green energy by 2025, with over 50 nations planning to achieve 100% green energy by 2050.
Endowed with abundant wind energy resources, China has a total wind energy resource reserve of approximately 32.26 billion kilowatts. The onshore wind energy reserve available for development and utilization is around 2.53 billion kilowatts, while the offshore wind energy reserve is approximately 7.5 billion kilowatts, totaling about 10 billion kilowatts. From 2016 to 2022, the wind power generation maintenance market in China has shown a year-on-year growth trend. In 2022, the market size reached approx. 35.7 billion RMB. As of the end of June 2023, China's wind power generation capacity is approximately 340 million kilowatts, showing a year-on-year growth of 17.2%. The average utilization of wind power generation equipment has accumulated to 1154 hours, a decrease of 58 hours compared to the same period last year.
During the development of wind power projects, the ability of a wind turbine to achieve optimal performance during its rated operation period is a crucial factor in assessing the success or failure of the wind farm investment. The wind power generation maintenance market spans the entire lifecycle of wind power equipment; from manufacturing, installation to eventual decommissioning, lasting 20-25 years. Quality wind turbines aside, life-long operational maintenance is critical. Large outdoor wind turbine blades face the following challenges in terms maintenance:
- Traditional manual basket monitoring methods are difficult, expensive, and involve extended turbine downtime, suitable only for detecting blade cracks and lightning strikes.
- The method of embedding sensors in the blades for monitoring, while enabling real-time monitoring without downtime, is highly difficulty and cost-intensive.
- Although the use of unmanned aerial vehicles (UAVs) for blade inspection is cost-effective, the turbine needs to be shut down, and real-time turbine monitoring cannot be achieved.
AI Vision Inspection for Prompt Maintenance and Reduce Cost
To address the aforementioned maintenance challenges and reduce customer operational costs, Chinese wind turbine equipment and solution providers propose integrating an AI visual inspection system into a comprehensive smart wind farm operations and maintenance. AI image monitoring solutions offer advantages such as low overall investment costs, the ability to perform real-time monitoring without downtime, large detection coverage, and high accuracy. This approach is most effective in proactively preventing wind turbine damage and maximizing power generation by monitoring turbine status in real-time.
Leveraging extensive real-case data, Chinese wind turbine equipment manufacturers have developed highly accurate AI models. The precision of ice accretion detection is over 95%, crack detection accuracy exceeds 95%, and lightning strike recognition accuracy surpasses 80%. Once an issue is detected, the system immediately issues a warning for prompt maintenance.
The AI visual inspection system is compact, allowing customers to directly install it in existing wind power equipment to optimize wind turbine efficiency without the substantial costs deriving from purchase of new large-scale equipment. No downtime is required for installation and operation. In cases with specific site constraints, Chinese wind turbine equipment and solution providers can tailor AI solutions for each wind farm, enhancing performance, increasing power generation, and extending turbine lifespan to elevate the overall value of wind farms.
The overall system installation and operation process are as follows:
- Install cameras on all new wind turbine models, offering customized blade image monitoring solutions even for third-party turbine units.
- Add the AI visual inspection system to the wind turbine, monitoring blade status and providing real-time digitized data.
- The monitoring system is centralized in the control room, enabling remote monitoring of equipment status and providing analysis reports.
- Installation on-site requires no wind turbine downtime, plug-and-play capable, with system operation completed within 1 hour.
- The AI models, post-training, can be remotely synchronized to edge systems for continuous monitoring.
- Remote real-time blade inspections are conducted to ensure optimal performance.
Key Benefits for AI Predict Maintenance of Wind Energy
- Retrofit Market Solution: The system belongs to the aftermarket, allowing customers to perform maintenance without replacing the entire wind turbine generator set. No turbine downtime is required.
- AI Image Monitoring: Utilizes AI image monitoring, providing real-time images of various parts of the blades through camera installation. Users can instantly monitor on-site conditions.
- Real-time Defect Detection: Image data is inputted in real-time into the AI system, which incorporates AI image recognition algorithms for instantaneous detection of blade defects, issuing rapid alarms for issues like ice accretion, cracks, and fractures.
Why Advantech
- Advantech offers an integrated hardware and software solution, reducing customer development costs.
- Advantech's MIC-711 system features a fanless, compact industrial design suitable for outdoor installation, ensuring long-term stable operation.
- Advantech provides edge AI analysis SDK, management platform software, and value-added services, allowing flexible and customized solutions according to customer requirements.