High-Pressure Cylinder Test for Airbag Inflation
10/4/2024
Project Introduction
The basic idea of airbags is that when a car is involved in a collision, steel cylinders filled with highly compressed gas rapidly inflate airbags in the center of the steering wheel, the dashboard, and sometimes other places, to cushion driver and passengers, reducing and preventing injuries. A high-quality automotive airbag system cannot ignore the quality of the reservoir cylinders, because if a cylinder were to burst, the high velocity gas might project cylinder fragments into the surrounding areas, injuring people and causing significant injuries.
Countries worldwide have established standards associated with the manufacture, quality, and testing of these high-pressure cylinders. Therefore, it is necessary to use a professional high-pressure airbag steel cylinder testing machine during the production process to conduct the relevant tests for cylinders in order to ensure their quality and safety.
System Requirements
The system’s steel cylinders must undergo all relevant cylinder verification tests during the manufacturing process. Among them, the two most important are fatigue and burst tests.
- The fatigue test must be able to conduct continuous tests by automatically adding and reducing pressure by pre-configured amounts.
- The system must be able to record the testing data and calculate the relative pressure and time curves.
Project Implementation
- IPC-240: Compact Industrial Computer Chassis for PCE-2000 Series CPU Board
- PCE-2132: LGA1200 10th Generation Intel® Core™ i9/i7/i5/i3 & Pentium®/Celeron® CPU Board for IPC-2 Series Chassis
- PCIE-1810: 500 kS/s, 12-bit, 16-ch Multifunction PCIE Card
System Description
Advantech provided a series of products to perform high-speed pressure and flow volume measurements as well as equipment control for this application case. The IPC-240 features a compact design, ideally suited for in-cabinet applications needing high computing power but fewer expansion slots. With dimensions of 195 x 150 x 230 mm, IPC-240offers powerful performance and reliability, equipped with 4 expansion slots for integrating diverse add-on cards.
In order to obtain accurate pressure data based on customer requirements, the PCIE-1810 in the industrial-grade computer was a high-speed analog input card that captured the changing pressure signals rapidly and continuously. Its 500Ks/S high-speed sampling rate and 12-bit high resolution performed rapid data acquisition 100 times faster than that of a PLC. When the test machine performs a pressurization and decompression fatigue test 10,000 times on a steel cylinder, the PCIE-1810 operates at a sampling rate of ten thousand times per second. This significantly enhanced sampling rate captures the changing pressure signals rapidly and continuously, thereby resolving the customers’ PC/PLC data distortion problems.
System Diagram
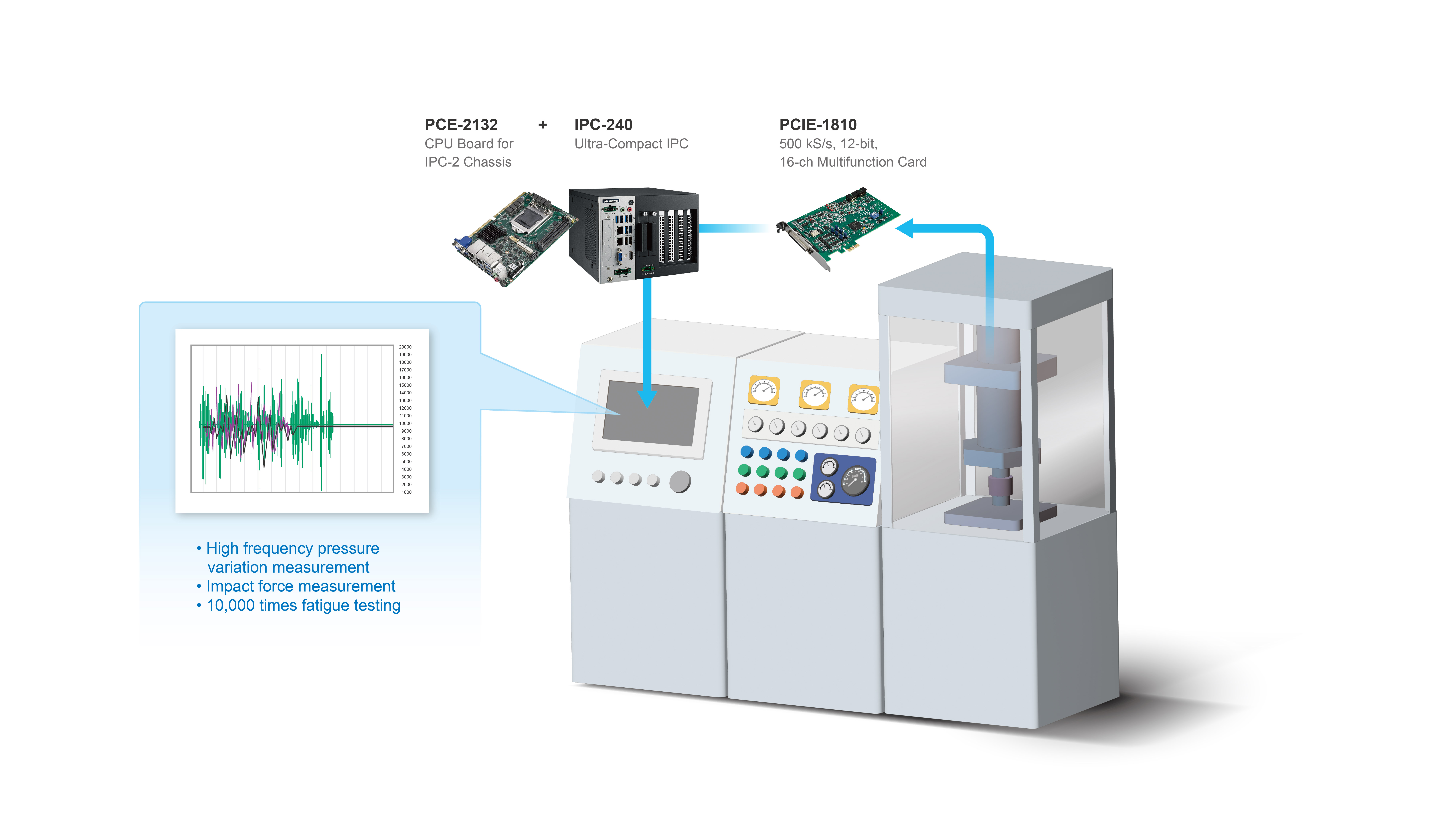
Conclusion
The effectiveness of airbags in vehicles relies on the integrity of the steel cylinders used to rapidly inflate them during collisions, mitigating injuries. To ensure the cylinders' reliability and safety, precise pressure and flow measurements are crucial. Advantech's high-performance products, such as the compact IPC-240 and the PCIE-1810 high-speed analog input card, provide essential capabilities for rigorous testing. These tools enable accurate, rapid data acquisition during extensive pressurization and decompression tests, preventing data distortion and ensuring the cylinders' quality. This technological advancement plays a critical role in maintaining the safety and functionality of automotive airbag systems.