The Next Leap of Digital Transformation in Manufacturing
12.08.2022
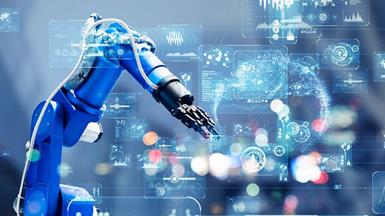
Introduction
The Fourth Industrial Revolution, also known as Industry 4.0, is the continuous automation and digitization of traditional manufacturing practices for more efficient and profitable growth. Although the term Industry 4.0 was coined in Germany, various countries are also developing digital transformation strategies and they subsidize companies who adopt digital transformation solutions. Manufacturing industry has long faced the pressure of labor shortages and rising labor costs, especially traditional industries, which cannot compete in terms of wages like the high tech industry can. The US/China trade war in 2018 and the pandemic from 2020, caused supply chain problems and protectionism has risen so the pace of digital transformation has to be accelerated.
What does industrial digital transformation mean?
The epidemic has accelerated the appetite for digital transformation. Because of the uncertainty of market demand and the risk of supply chains, many senior managers require real-time information, and because of the reorganization of the supply chain, competition has become more intense. Companies are also uncertain about how to go about digital transformation. Through a good understanding of trends in technology, business models, consumer behavior etc., enterprises can discover new opportunities and future development directions. Through digital transformation they can successfully convert challenges into new business opportunities and create sustainable value for their enterprise.
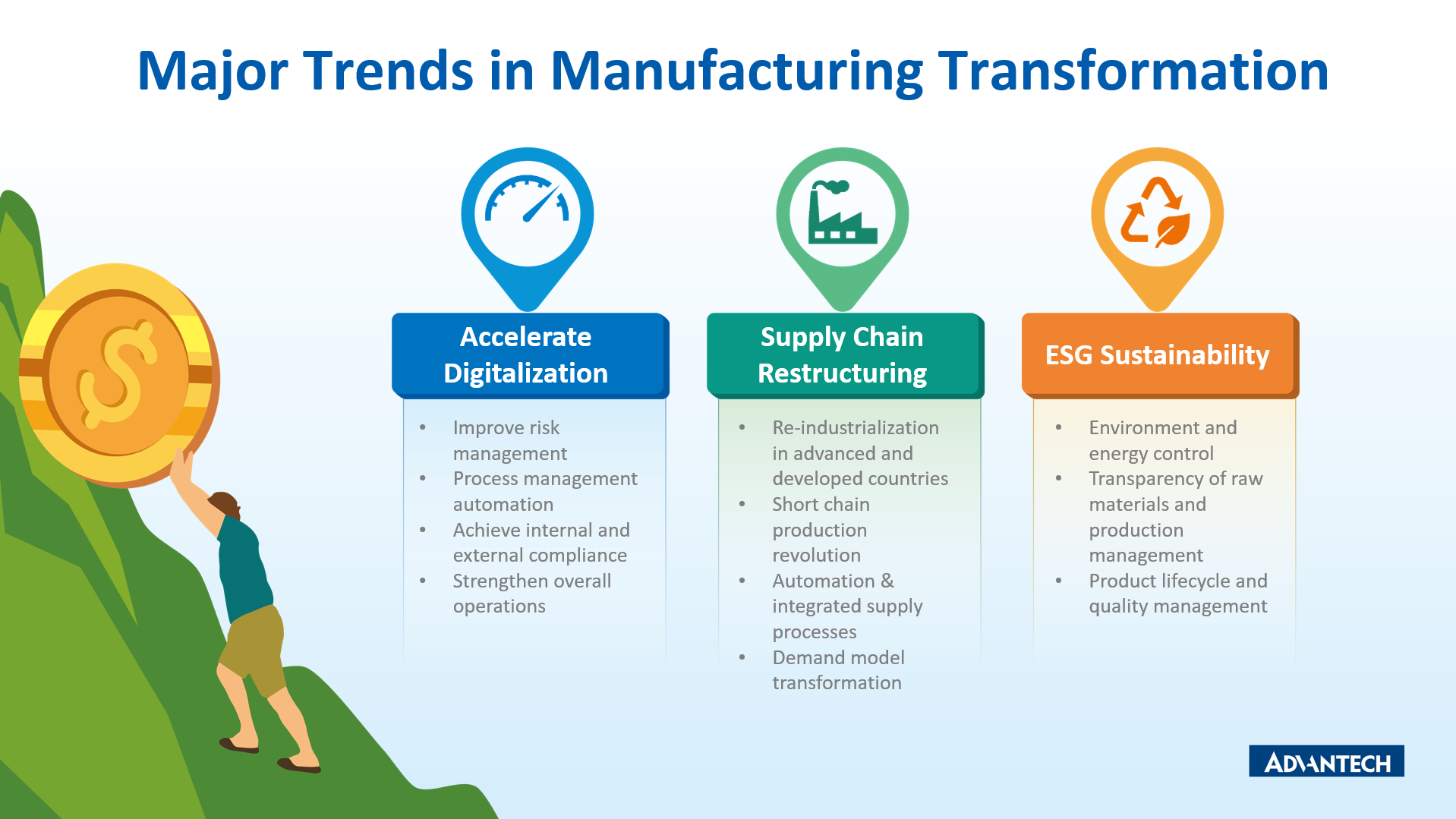
Accelerating digital transformation improves the automation of process management and the transparency of information and data, as well as strengthening overall operations. In the past, manufacturing took labor costs as their sole consideration, but because of the epidemic, the trends of the market supply chains has changed significantly. The issue of manufacturing cost has now been elevated to end-to-end benefits. Procurement strategies of enterprises is also changing and accelerating this digitalization process. This will bring great advantages to the visibility of the supply chain and help reduce supply risk to ensure a short-chain production revolution.
Why should the transformation of industrial digitization begin as soon as possible?
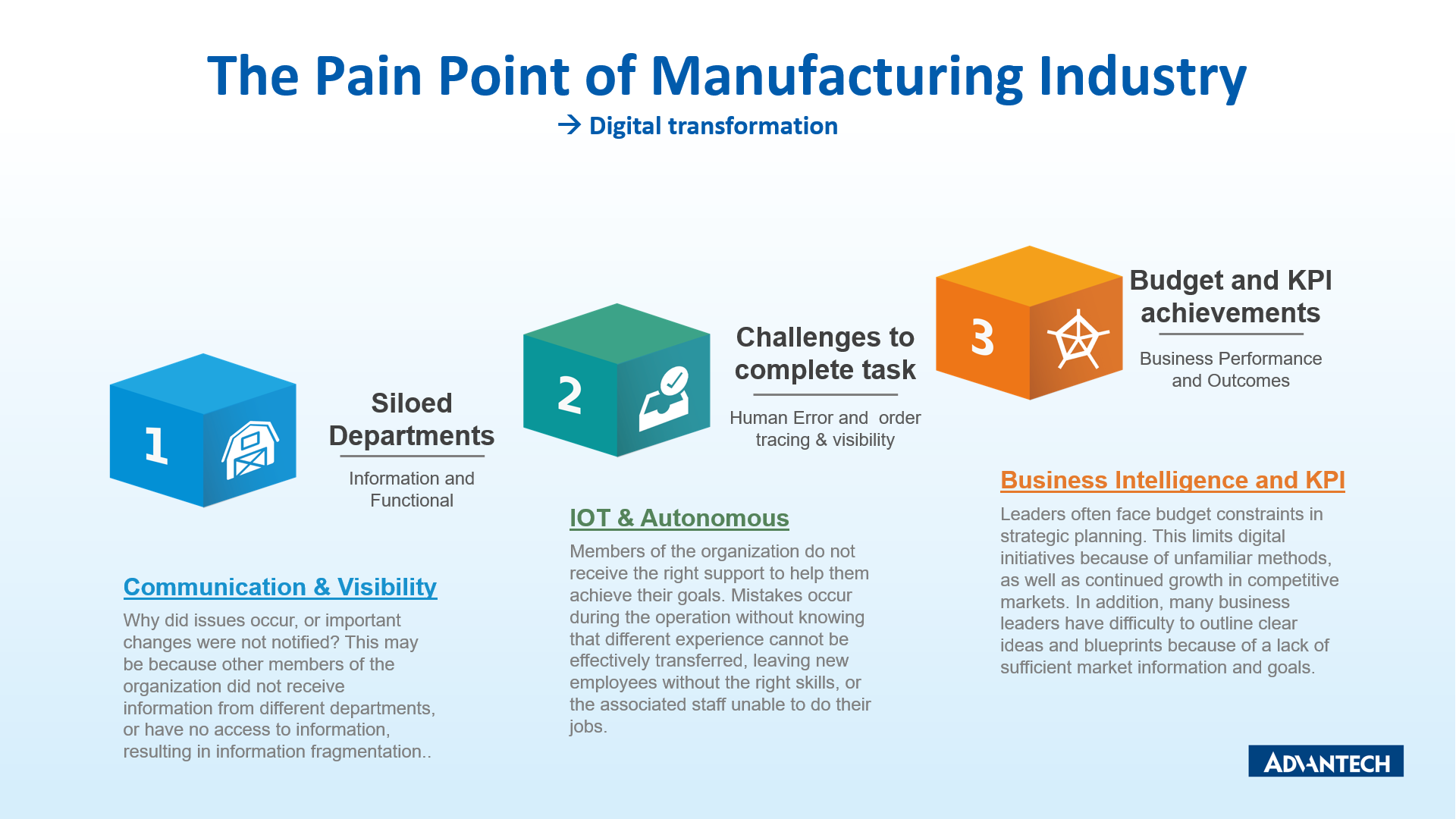
Combining lean manufacturing and digitization, with an emphasis on cost reduction, a focus on eliminating waste, and optimizing processes through customer demand, has played an important role in increasing the efficiency of the entire organization. Although lean manufacturing originated in factory production, its core principles can be found in a variety of organizations and applied in many different ways. Lean manufacturing and digitization can play a role in any field because it provides a data-driven approach to decision-making that emphasizes in root cause analysis and tracking. Lean manufacturing and digitization is the best approach for quickly identifying hidden problems and creating continuous improvements.
How should digital transformation be carried out?
Digital maturity assessment enables managers to determine where their organization is on the digital transformation journey, and based on the results of the assessment, set goals and a path to achieve digital transformation. The use of digital maturity assessment determines where you are, where you need to go, and how quickly you need to get there.
The Digital transformation process is divided into three directions, intelligent automation, intelligent optimization, and intelligent factory transformation:
- Intelligent Automation is the process of developing and transforming from analog to digital, from human operation to automated operation to enhance the value of productivity.
- Intelligent Optimization focuses on production issues, equipment issues, or energy sustainability issues to achieve business objectives. This includes improving internal or external business processes, production efficiency in all areas, and giving employees the data they need to better understand the direction of target improvements to deliver a better customer experience.
- Intelligent Factory Transformation unleashes the untapped potential with the tools and applications necessary for business intelligence (BI). It takes advantage of the most appropriate digital developments to benefit from the huge quantities of digital data in enterprises and how they evolve.
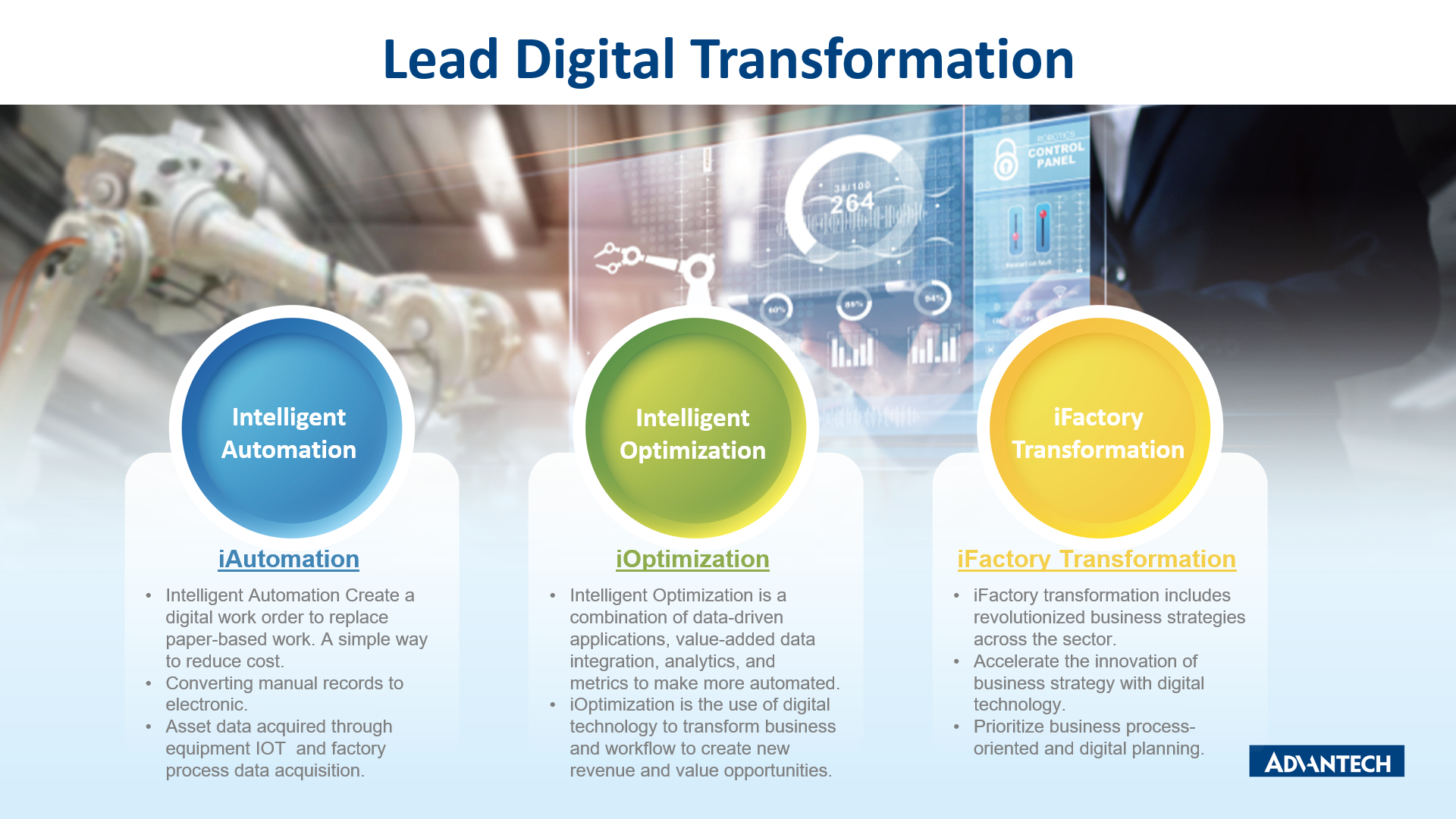
• Intelligent Automation: reduces downtimes, fault detection, and diagnosis problems
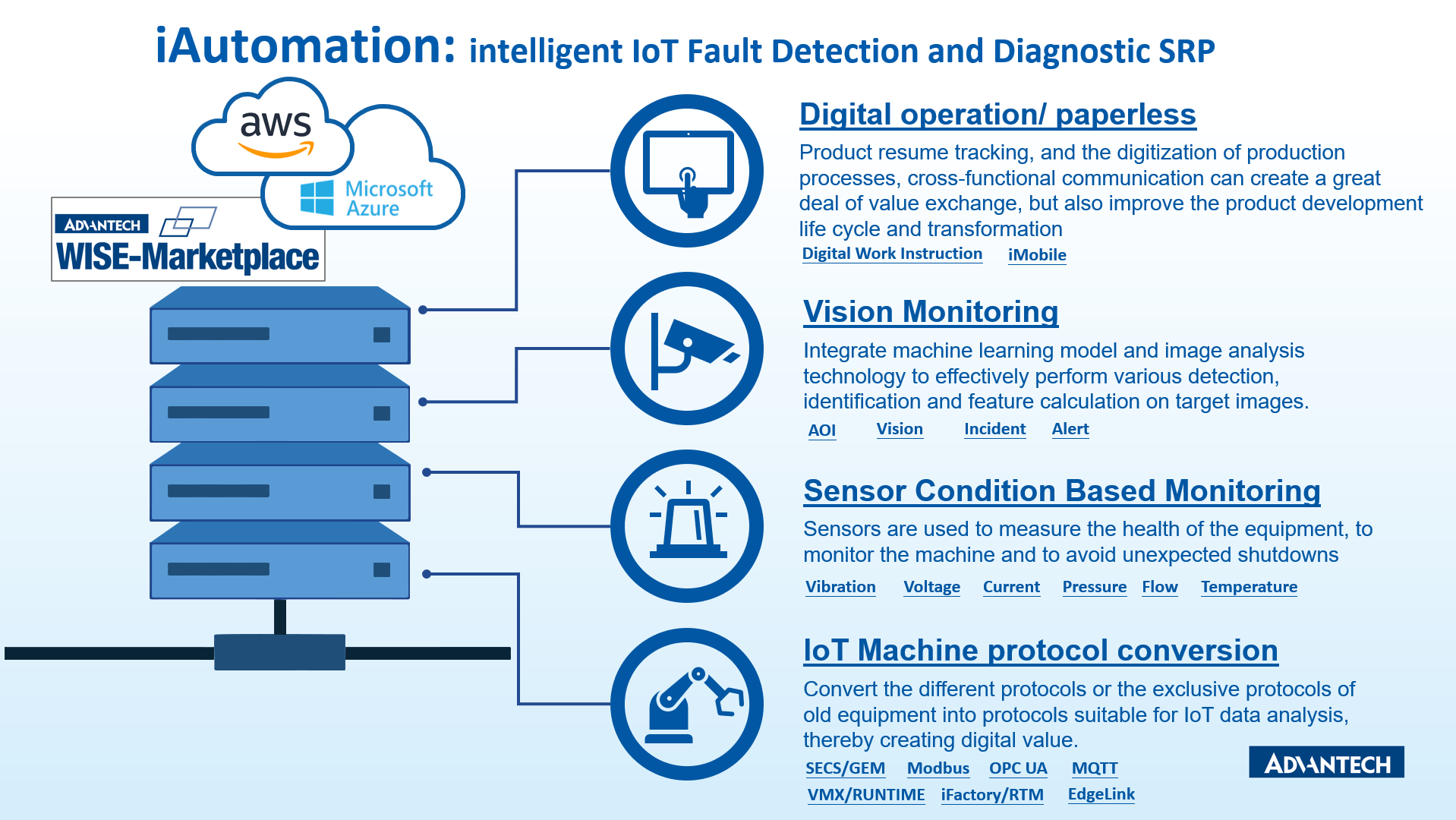
• Intelligent Optimization: saves labor costs and manufacturing overheads
Process manufacturing consists of batch production and continuous production modes. Typically, process-manufacturing equipment are dedicated machines that are difficult to switch to other use. Combined with an enterprise's information management system, the continuity and accuracy of production will be assured from customer services to supply chain logistics and production output.
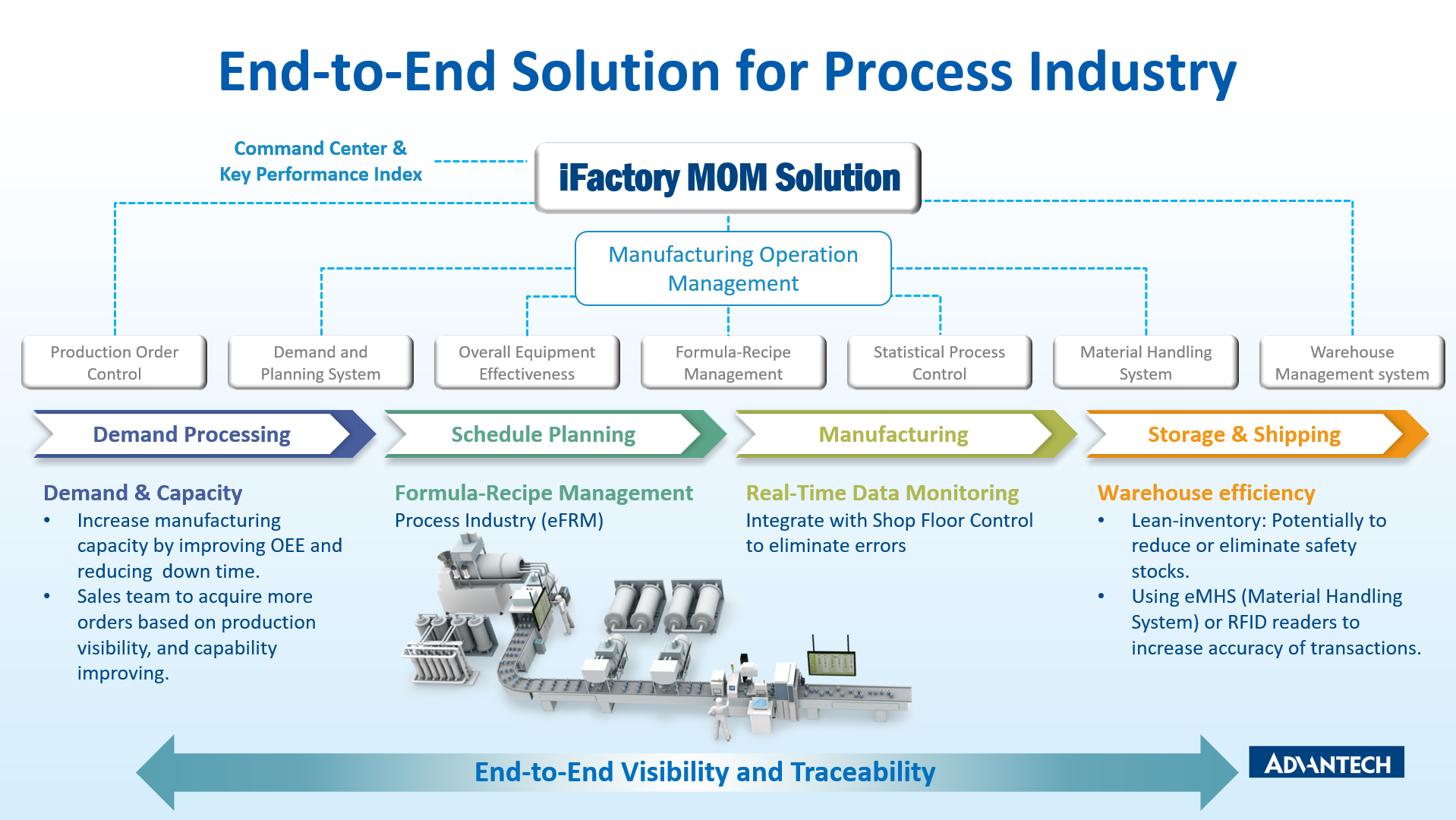
Saving labor costs and manufacturing overheads is always the key to success for discrete manufacturing. Digital production in workflow automation improves visual management tracking and timely resolution of product malfunctions or equipment anomalies. The combination of Andon and shop floor management with Manufacturing Operations Management (MOM) manufacturing operations management system, connected to MES through DataConnect, means this virtual data lake simplifies data usage for IT teams. Industrial engineers and plant managers can easily use automated data processing to check production line balance and allow them to follow lean processes, plus six Sigma standards, to increase output and efficiency.
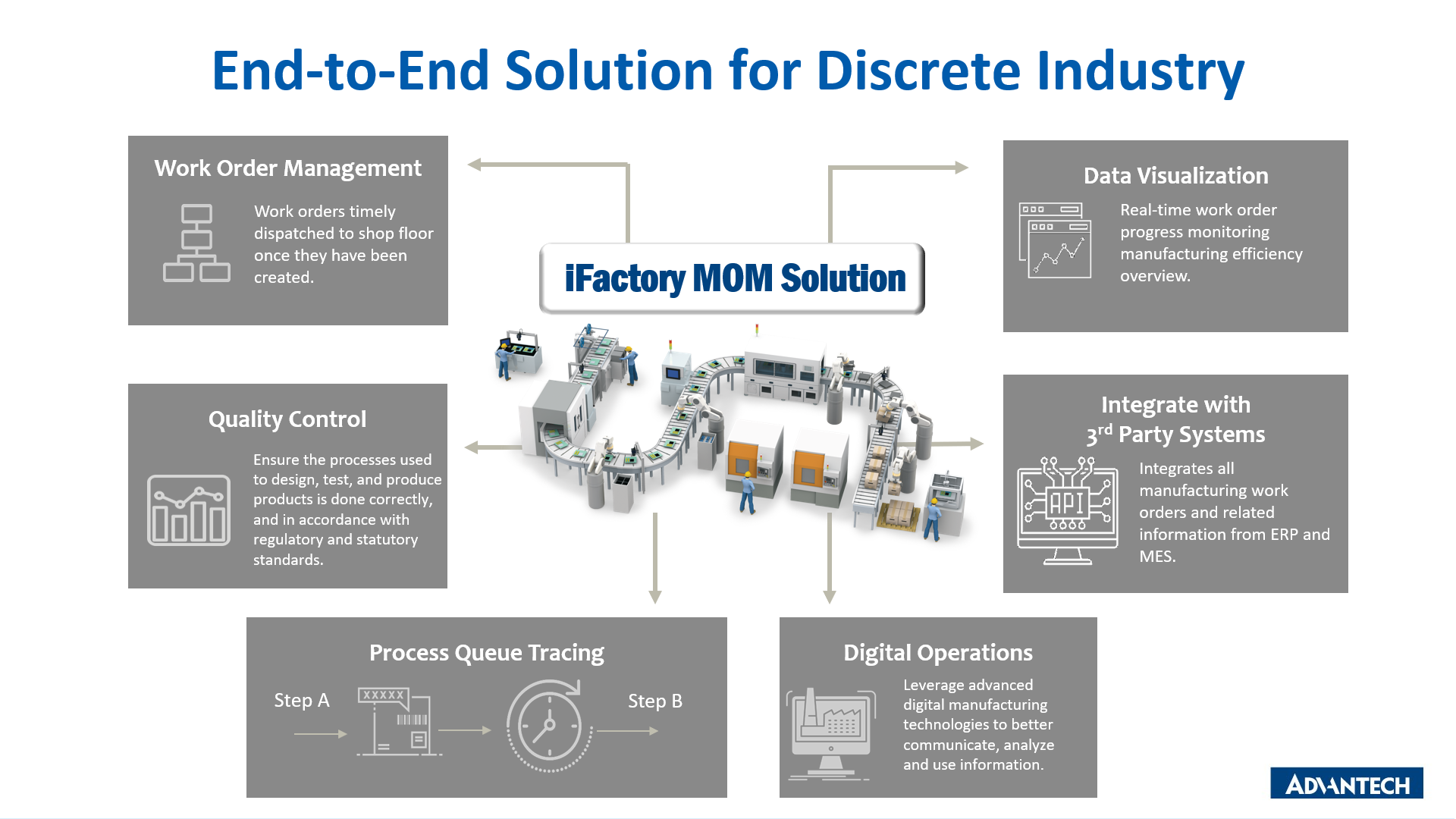
• iFactory Transformation: enjoy the power of big data to accelerate business digital innovation
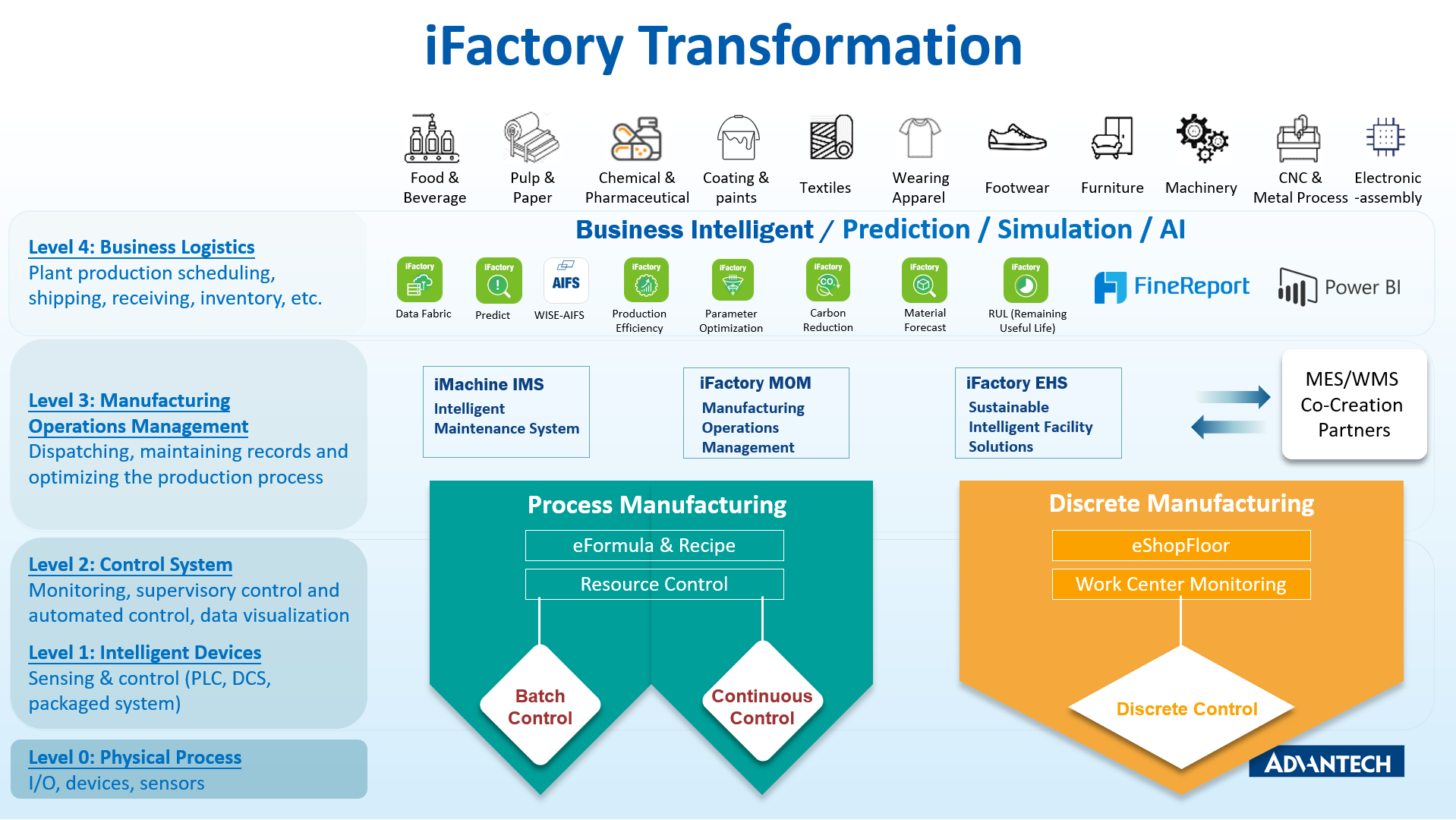
Industrial Digital transformation, how to reduce the probability of failure?
Many systems are used in manufacturing, including ERP/ MES/ warehouse management systems/ or supply chain systems. However, most of them are legacy systems that cannot be easily deployed or scaled, so knowing how to quickly generate value, upgrade applications, and change according to the business situation is an important consideration.
The adoption of containerized architecture can be said to be an important breakthrough in the cloud platform. Applications can be deployed in public or private clouds and system integrators can use the infrastructure to create their own innovative digital solution with their intellectual property protected. This is the best architecture to lead the digital transformation from A to A+.
Advantech iFactory offers digital transformation applications that dramatically reduce customer development times. They accelerate OT/IT capabilities and provide a variety of customized templates to accelerate the deployment of industrial applications to ensure the maintainability and expansion flexibility of all software and systems. This in turn allows companies without IT teams to quick-adopt, or companies with IT/AI prediction teams to enhance data analytics and subsequent growth planning expansion through data analytics in the data lake.
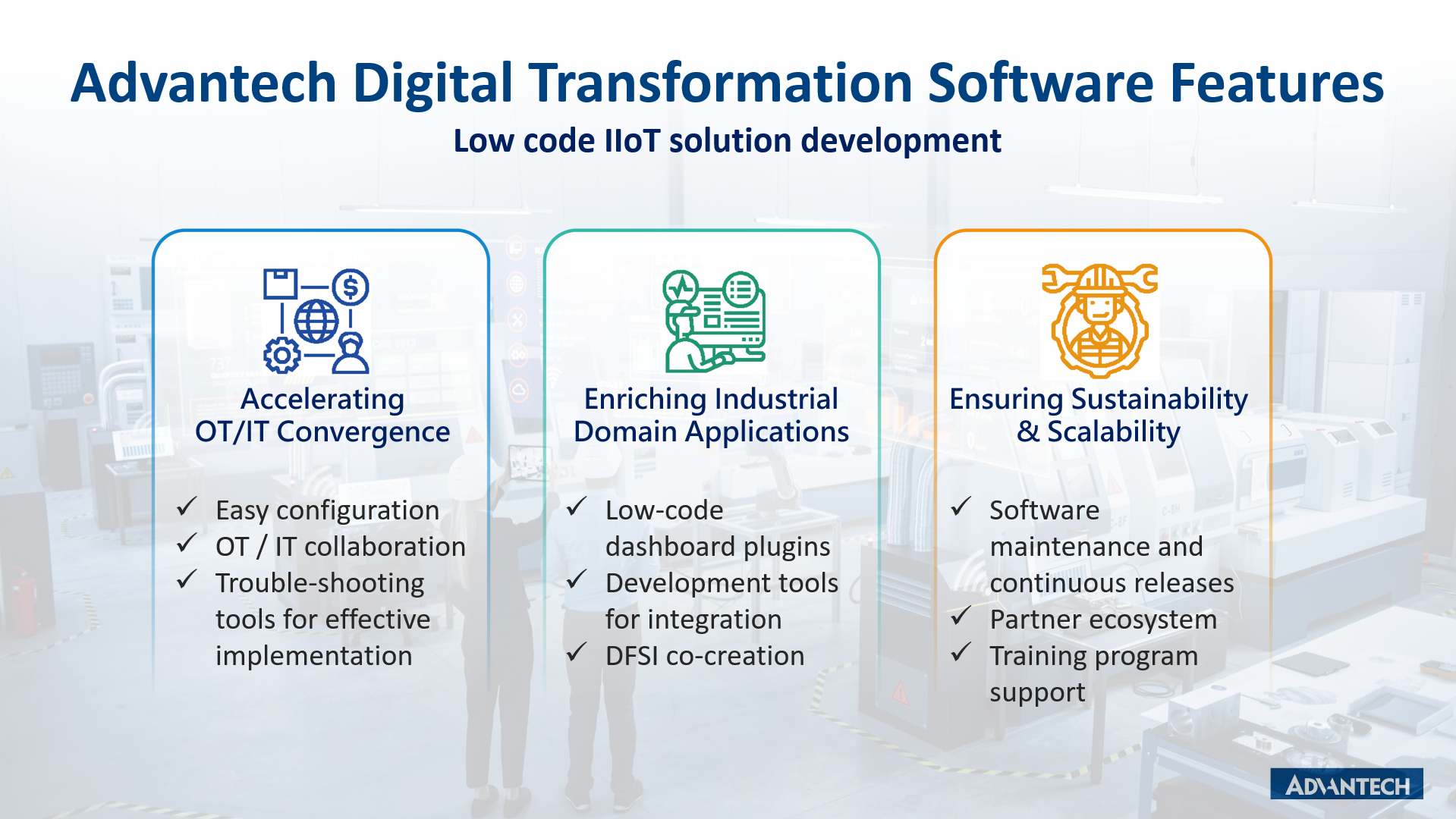
Perhaps your company has not yet started their digital transformation, and may lag behind the competition, but it is also possible that now is the best time and this is an advantage. By understanding the clear purpose of your business, insights can be gained, so that in the future, research times can be reduced and the benefits of industrial digital transformation can be used to transform your business.
Resources
WISE-Marketplace
Advantech WISE-Marketplace provides pre-tested domain-focused I.Apps ready to integrate directly into your IoT scenarios. Browse the collections to see...