Intelligent Logistic Automation: AGV Computing Power for Autonomous Forklift
5/02/2024
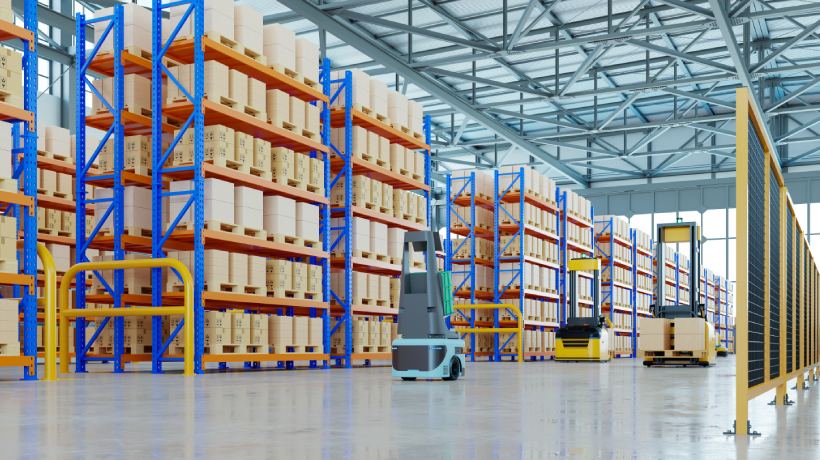
Introduction
The global industrial automation market is rapidly growing thanks to the increased development of intelligent technology. According to the latest market research study by RESEARCHANDMARKET, the global automated AGV and AMR market is projected to reach around USD 20 billion by 2028, experiencing growth rates of approximately 22% for AGVs and 37% for AMRs.
A leading manufacturing equipment provider located in China offers logistic solutions for the material handling business and has developed autonomous forklift vehicles to provide advanced, efficient, flexible, and cost-saving solutions for the manufacturing, logistics, and warehousing industries. The autonomous forklift can significantly reduce labor costs, mechanical damage, and damage costs by delivering goods more efficiency than traditional conveyor systems and forklifts driven by workers.
Project Requirements
The Chinese client is a large manufacturer of hand pallet trucks with over 10 years of expertise in producing Class 1, 2, and 3 forklifts in China. Dedicated to providing global solutions for material handling, the company is at the forefront of innovation, particularly in the realm of autonomous guided forklifts. Their latest products boast cutting-edge features, including a state-of-the-art navigation and localization system integrated with 360° Lidar and cameras, operating on advanced mobility technology. These autonomous forklifts showcase stable navigation and localization capabilities, enhancing intelligent distribution across various scenarios.
Notably, the UNO-238 stands out, featuring a robust Intel® Core™ i CPU with formidable computing power, supporting seamless wireless communication and CAN Bus 2.0 (Controller Area Network 2.0). The utilization of CAN Bus technology significantly streamlines communication among electronic controllers (ECUs), also known as “nodes.” This allows them to communicate and cooperate with each other without the help of a host computer to interpret or convey in-vehicle information. This adoption efficiently reduces weight and fuel consumption while simplifying the system’s structure. This breakthrough solution not only cuts costs but also elevates product quality and overall performance efficiency for autonomous forklift manufacturers, making it a pivotal asset for their operations.
Project Implementation
- UNO-238, Compact IoT Edge Computer with 8th generation Intel® Core™ i CPU
- EKI-1361, Industrial Wi-Fi Client
- EKI-6333AC-2G, Industrial Wi-Fi Access Point
System Description
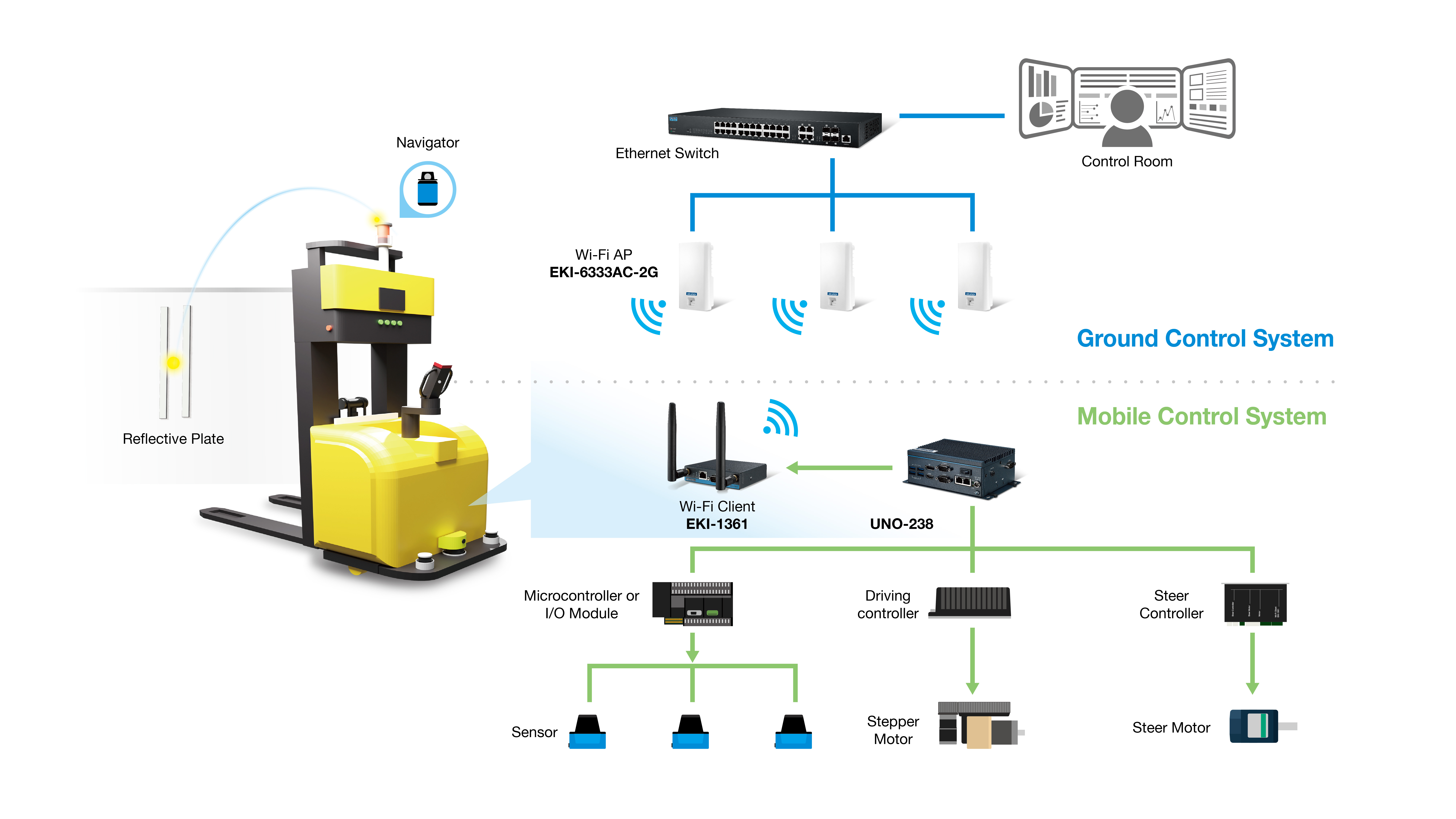
Advantech’s UNO-238 acts as a host to process data and execute instructions for the autonomous forklift. Serving as the central brain, the UNO-238 interfaces with various modules, including steppers, navigators, driving controllers, GPS, sensors, and steering controllers to form a robust mobile control system with precise handling and movements. In this case, the navigators on the system, equipped with sensors, such as Lidar or cameras, use these strategically positioned reflective plates along the automatic forklift's route as navigational markers. When the sensors detect these reflective plates, they provide crucial positioning and orientation information to the navigator. On the other hand, the driving and steer controllers receive instructions from the UNO-238, translating them into motor control signals for the vehicle's movement and direction. These controllers work in tandem with the steppers to execute precise and controlled motion. Overall, Advantech’s UNO-238 helps raise the processing stability and efficiency for a competitive price, allowing AGV forklifts to connect to sensors for contour-based navigation and make different guided path decisions on their own.
To provide wireless communication capabilities, the UNO-238 is equipped with the EKI-1361 series of fast-roaming wireless clients, providing essential technology for communication between AGVs and the central control system. EKI-1361 will be remote connected via EKI-6333AC-2G, Wi-Fi access point, to the ground control system. This configuration enables a reliable and efficient flow of information between the ground control system and the AGVs. The Wi-Fi client facilitates bidirectional communication, enabling the AGV to receive commands and transmit its operational data, while the Wi-Fi AP acts as the intermediary, managing the network connectivity for the fleet of AGVs within the system. This communication loop ensures that the AGVs receive real-time instructions, updates on tasks, and adjustments to their routes, all while transmitting data on their status and operations to the central control system. The connection between these systems forms a cohesive network that enables efficient coordination and control of the AGVs within an industrial or logistical setting.
Conclusion
The evolving complexities within warehousing, manufacturing, and distribution processes necessitate the integration of highly stable autonomous forklift technology. AGV implementation alleviates the strain of labor shortages and provides cost-effective solutions. The client’s autonomous forklifts, empowered by Advantech’s UNO-238 Compact IoT Edge computer, can be widely used in low-height racking fields. These forklifts stand out as optimal solutions for material handling operations, effortlessly lifting and delivering goods, automating inventory stocking and retrieval. Leveraging advanced navigational technology like SLAM, they enhance inventory management effectiveness while significantly reducing errors and minimizing accidents.