Maximizing Productivity in the Surface Treatment Industry Using Smart Technology
2021/8/24
Abstract:
Surface treatments are a form of a protective coating that extends the lifespan of equipment by protecting parts from wear and abrasion. These treatments play a key role across several industries, including the automotive, aerospace, construction, container, electrical, medical, and industrial equipment industries.
Partner: Braspo Pintura Industrial, ECO Automation | Region: Brazil
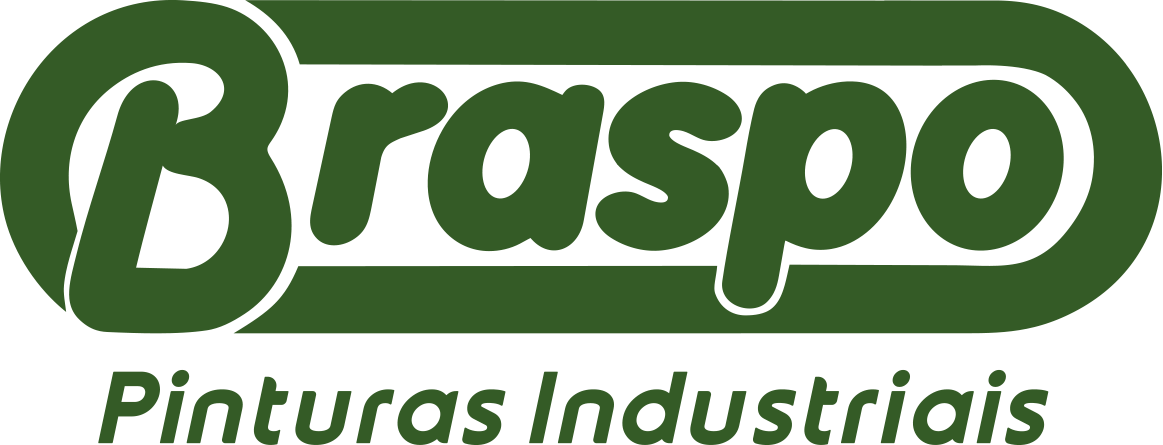
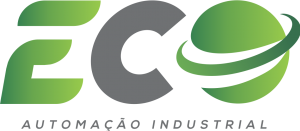
Introduction
Surface treatments are a form of a protective coating that extends the lifespan of equipment by protecting parts from wear and abrasion. These treatments play a key role across several industries, including the automotive, aerospace, construction, container, electrical, medical, and industrial equipment industries. Protective coatings not only guard these parts against these issues but also provide increased structural integrity. Therefore, using the right surface treatment is vital as it can significantly increase a part’s lifespan, cut downtime, and reduce overhead costs.
Surface treatment means altering the molecular constitution of a surface to interact with an adhesive, ink, coating, paint, or another surface to create a strong bond between them. Surface coatings include paints, drying oils and varnishes, clear synthetic coatings, and other products, and their primary function is to protect the surface of an object from the environment. In addition, these products can enhance the aesthetic appeal of an object by accentuating its surface features or concealing certain features. Furthermore, the surface and interfacial tensions play a crucial role in coating quality.
The quality of surface treatments has improved as a result of manufacturing processes becoming more advanced due to an increase in novel materials, innovative structural geometries, and automated processes. Therefore, manufacturers need to initially determine the performance parameters crucial for satisfying customers’ needs and then develop a surface treatment to meet those requirements. However, meeting these requirements can be challenging and necessitates further research alongside employing the best tools to measure the performance parameters. Additionally, creating and optimizing surface treatment processes is one of the most difficult challenges faced by manufacturers. Therefore, a robust and effective surface treatment process will involve a smart system to ensure an in-line, fast, easy, and accurate verification method.
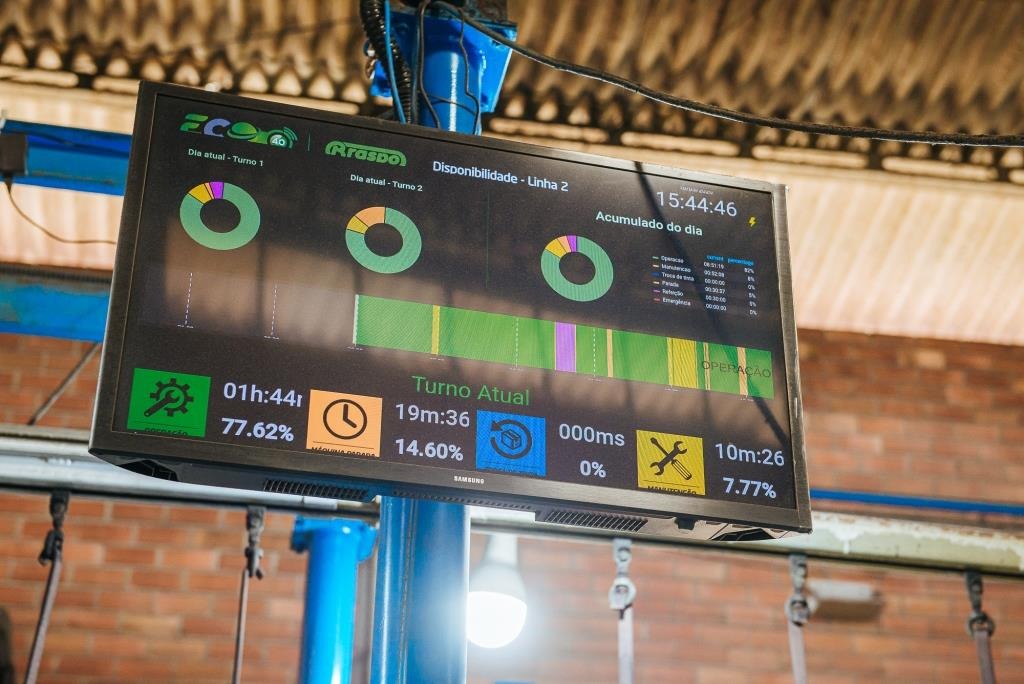
System Requirements
Braspo Pinturas Industrials specializes in surface treatment (painting), bringing brand innovation and excellence in all its processes whilst maintaining an undeviating commitment to ethics, quality, and respect for employees, suppliers, and customers. With substantial knowledge in the field and through techniques, from the choice of the hooking device to the most suitable surface treatment process for the client’s segment, Braspo offers distinctive solutions which ensure the protection and quality of the product.
The company faced the challenge of monitoring the status and performance of their painting cabins effectively and efficiently. The method being used involved physically going into the production lines to know the status of the specific process. Thus, the project focused on designing a platform that provides information on the machine availability as well as performance status with the following criteria:
- 24/7 availability with real-time performance tracking
- Reliable, easy, and simple to use
- Low-cost
- Ability to measure the quantity of natural gas being used
- Adaptable and easy to replicate across other lines
System Description
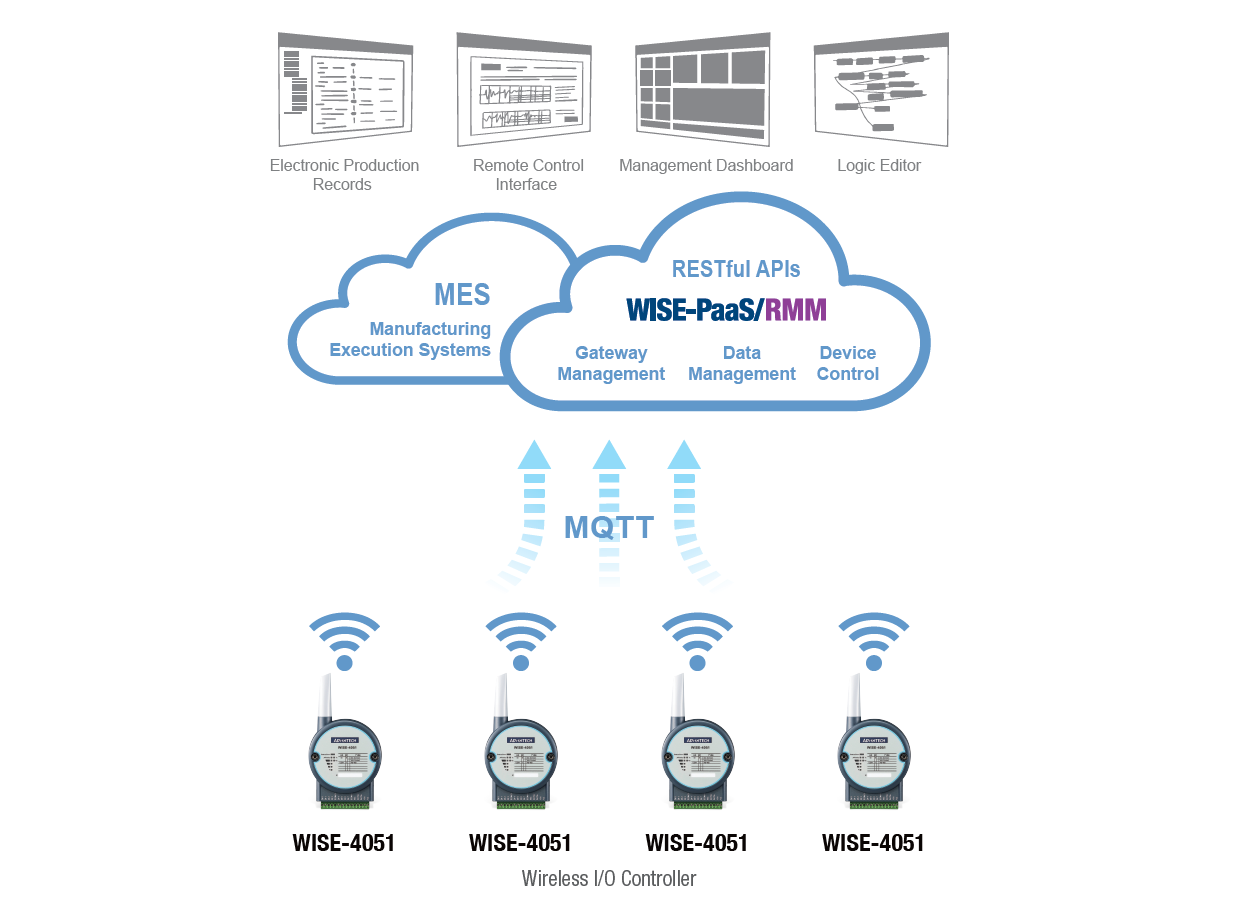
The WISE-4051 used is an Ethernet-based wireless IoT device integrated with IoT data acquisition, processing, and publishing functions, as well as various I/O types. The WISE-4051 provides data pre-scaling, data logic, and data logger functions, which allows data to be accessed via mobile devices and be securely published to the cloud anytime from anywhere. The WISE-4501 gateway was used to collect data directly from the machine panel using only digital inputs.
The operation signal was collected through the inverter signal. The ON/OFF signal is derived from the machine’s 24VDC power supply. The Ink Swap signal was generated from a proximity sensor to detect the metallic plunger on the valve. As for the hook count, a different proximity sensor was installed in the painting monorail to provide the mechanism to account for the number of hook passes on the point. Not to be forgotten, the maintenance signal was designated to be manually triggered by the maintenance team.
Project Implementation
- WISE-4051 – Wireless I/O Controller
- Proximity Sensor
Conclusion
Most products are coated either for functional or decorative reasons and as a basic requirement, they should form a uniform, defect-free coating on a surface. The coating provides corrosion protection as well as an opportunity to meet the increasing requests for the individualization of products. However, the industry faces challenges with huge downtime as a result of ineffective performance monitoring processes, which highlights the need for a smart technological solution. That’s where Advantech comes into play.
The smart system designed and implemented was in line with the customer’s requirement of 24/7 machine availability and real-time performance status. While, the technological solution entails the use of an Ethernet-based wireless IoT device that collects data, and can automatically push the collected data to a platform providing real-time information.
As a result of the solution implementation, process availability increased from 58% to 85% in five months, providing the customer with data to enable process improvement. In addition, the enhanced performance and 24/7 operation of the system allowed for a more efficient and effective operation while reducing downtime, creating an opportunity for a 3rd shift. Advantech solutions brought simplicity to complex problems, which translated into a strong competitive position for the company, enabling it to move forward with a new, more efficient, and durable solution.